Rotary Screen Printing Machine |
BENEFITS |
SALIENT FEATURES |
- COST SAVING
- TIME SAVING
- LABOUR SAVING
- SPACE SAVING
- WATER SAVING
- COLOUR SAVING
- FAST PAYBACK
- ENVIRONMENT FRIENDLY
|
- Each screen is independently driven
- Printing paste is fed by special pumps individually to the different screens
- print paste level in the rotary screen is automatically and constantly controlled
|
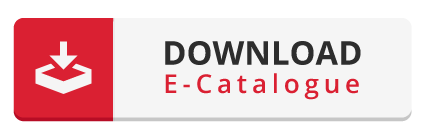 |
|
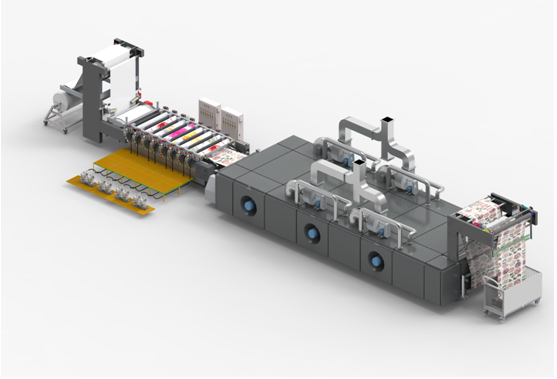 |
|
|
PRINTING ZONE |
 |
Infeed options
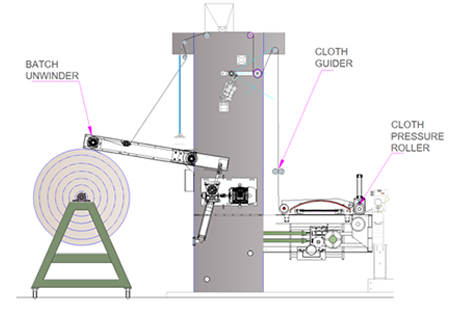 |
|
|
Features |
- Batch unwinding
- High entry for crease less fabric feeding
- Cloth tensioning device
- Electromagnetic cloth guider
- Band plate with electric heater
- Dust collector (optional)
- Knitted, lycra& other delicate fabrics uses standard spreader unit (optional)
|
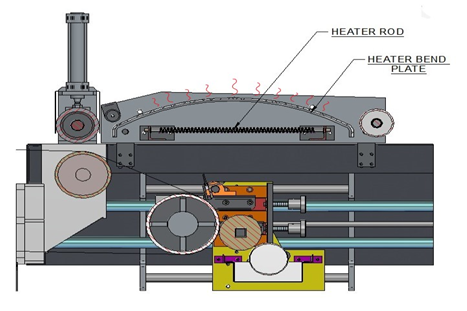 |
|
|
PVA-GLUING UNIT (OPTIONAL) |
- PVA glue application unit through rubber roller and segment device.
OR
- Adhesive applying application unit and adhesive stripping unit for fine layer adjustment rubber squeegee.
|
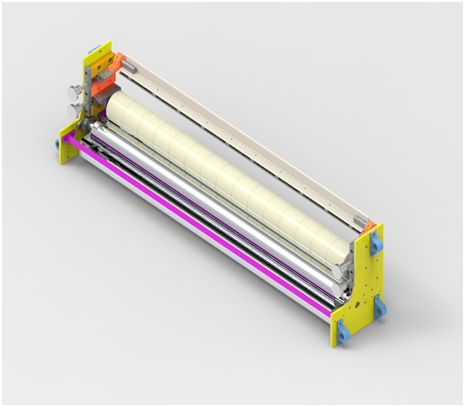
Gluing unit with stainless steel tray and segment type brush to adjust fabric width |
|
|
Rotary SCREEN PRINTING MACHINE TECHNICAL DATA |
1 |
Standard Printing width |
1280, 1620, 1850, & 2250 |
2 |
Printing repeat |
64, 82, 91.4, 101.8 cms. |
3 |
Printing speed |
8 to 80 mts./min. |
4 |
Nos. Of colours |
8,10,12,16,20,24 |
5 |
Suitability of cloth |
Cotton, Viscose, Polyester, Knitted, Lycra, etc. |
6 |
Drive of the M/C |
A.C. variable-inverter drive & All servo drive |
7 |
Dryer type |
Oil / Gas / Steam heated |
|
Drive Option : |
- A.C. Variable-inverter drive
- All servo individual head servo motor with drive for most accurate & speedy design change over
|
SQUEEGEE SYSTEM |
A squeegee is a tool with a blade that removes or controls colours across surfaces.
A tool possessing a wooden or metal handle to which is attached a thin, flexible rubber or plastic blade. A squeegee is used in screen printing to force ink through the printing screen and onto the substrate |
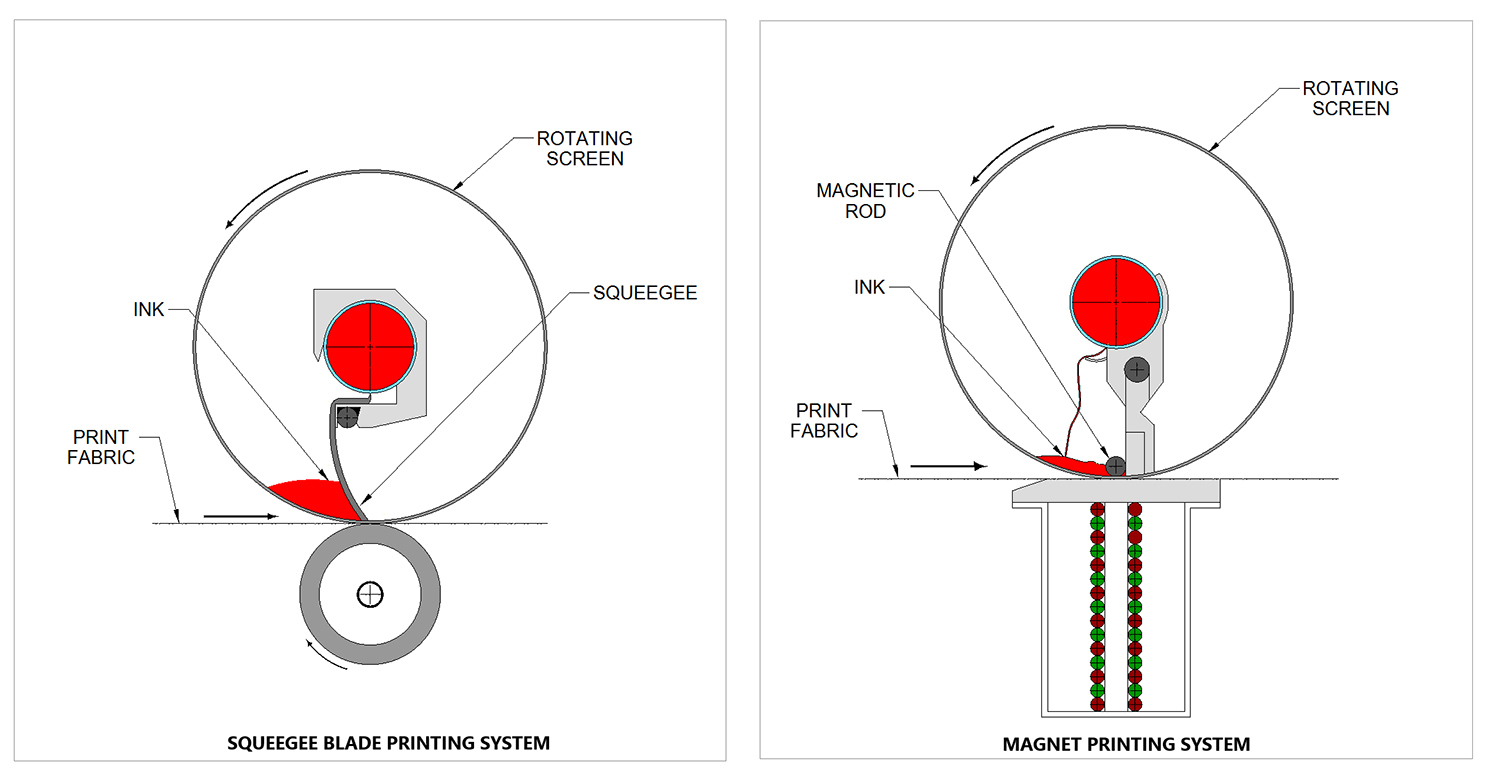 |
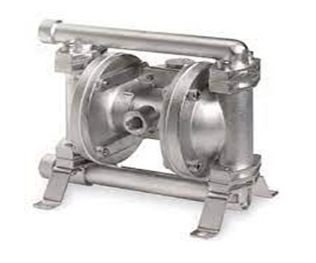
Stainless steel body diaphragm pump for colour feeding system. |
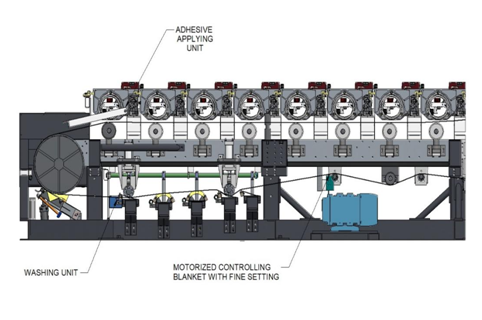
Blanket washing unit
Sponge type blanket washing unit with spray pipe and recirculation system to reduce water consumption.
|
|
|
HIGH EFFICIENCY DRYER |
A dryer through which the printed cloth passes. A dryer is needed when printing with heat set inks which dry and set only with the application of heat |
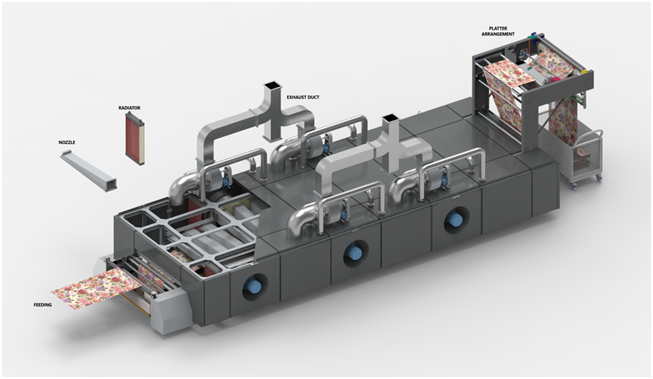 |
|
|
|
OIL / STEAM HEATED DRYER |
WITH HIGH EFFICIENCY DOUBLE RADIATORS FOR EACH SECTION OF DRYER
- 4 RADIATORS PER CHAMBER EANABLES VERY HIGH DRYING CAPACITY & FASTER PRODUCTION.
|
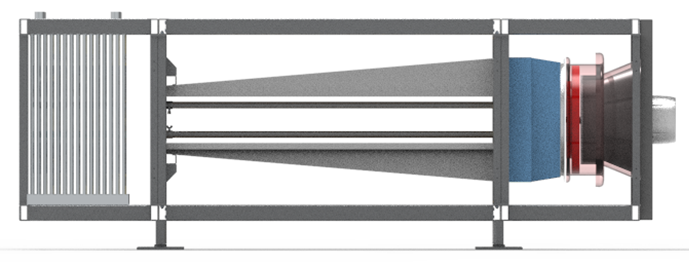 |
|
|
GAS HEATING |
WITH CLOSE CIRCUIT DESIGN OF DRYER TO ENABLE VERY FAST GAIN OF DRYING TEMPERATURE WHICH ENSURE HIGH EFFICIENCY.
- UNIQUE FEATURES
- HIGH EFFICIENCY DRYER
- THE INGENIOUS NOZZLE SYSTEM
- ADJUSTABLE INVERTER-CONTROLLED AIR FLOW ENSURE UNIFORM TEMPERATURE DISTRIBUTION
- EASILY REMOVABLE LINT FILTERS AND NOZZLE FOR CLEANING
- SUPERIOR INSULATION PANELS FOR ENERGY SAVING
- MODULAR DESIGN OF CHAMBER
|
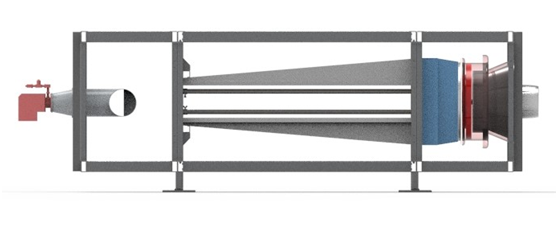 |
|
|
TYPICAL SCHEMATIC DIAGRAM FOR SCREENOTEX ENGINEERS RSPM |
|
|
|
|
|